What Are The Considerations In Designing Electrical Systems For Mining And Mineral Processing?
Mining and mineral processing are critical aspects of modern life. These industries are responsible for extracting and processing the materials we rely on to fuel our economies and power our homes. However, these industries are also some of the most energy-intensive and environmentally impactful operations in the world. As a result, improving the efficiency and sustainability of mining and mineral processing is a top priority for many companies and governments. One of the key elements in improving the efficiency and sustainability of mining and mineral processing is the use of oxygen generators. These generators are used to produce oxygen on-site, eliminating the need to transport liquid or compressed oxygen to the site. This saves both time and money, as well as reducing emissions associated with transportation. But how do oxygen generators actually work? The process is fairly simple. Oxygen generators use a technique called pressure swing adsorption (PSA) to extract oxygen from the air. Essentially, the generator takes in air and uses filters to remove impurities like carbon dioxide and water vapor. The purified air is then compressed and sent through containers filled with a material that adsorbs nitrogen. This leaves behind a stream of highly concentrated oxygen that can be used for a variety of applications. One of the most common uses for oxygen generators in mining and mineral processing is in gold extraction. The process of extracting gold from ore requires the use of cyanide, which can be dangerous to handle and dispose of. However, by using oxygen generators to produce oxygen on-site, companies can replace some of the cyanide with oxygen, reducing the need for this hazardous chemical. Oxygen generators can also be used in other aspects of mineral processing, such as in the production of steel. In steel manufacturing, oxygen is used to increase the temperature of the furnace, allowing for more efficient, energy-saving production. By using oxygen generators to produce on-site oxygen, steel manufacturers can reduce their energy costs and emissions. Another benefit of using oxygen generators in mining and mineral processing is their flexibility. These generators can be customized to fit the specific needs of a particular operation. For example, some generators can produce very high purity oxygen, which is necessary for some industrial processes. Others can produce smaller volumes of oxygen for smaller operations. One major challenge facing the mining and mineral processing industries is the need to reduce their impact on the environment. These industries are some of the largest sources of greenhouse gas emissions, and they often use large amounts of water and energy. By adopting technologies like oxygen generators, companies can significantly reduce their carbon footprint, as well as their use of natural resources like water. Of course, there are some challenges associated with using oxygen generators as well. These generators require a significant upfront investment, and they require ongoing maintenance and monitoring to ensure they are functioning properly. Additionally, some operations may not have the space or infrastructure necessary to support an oxygen generator. Despite these challenges, it's clear that oxygen generators have significant potential to transform the mining and mineral processing industries. By providing a reliable, on-site source of oxygen, these generators can improve efficiency, reduce costs, and protect the environment. As these industries continue to grow and evolve, it's likely that more and more companies will turn to oxygen generators as a critical tool for success.
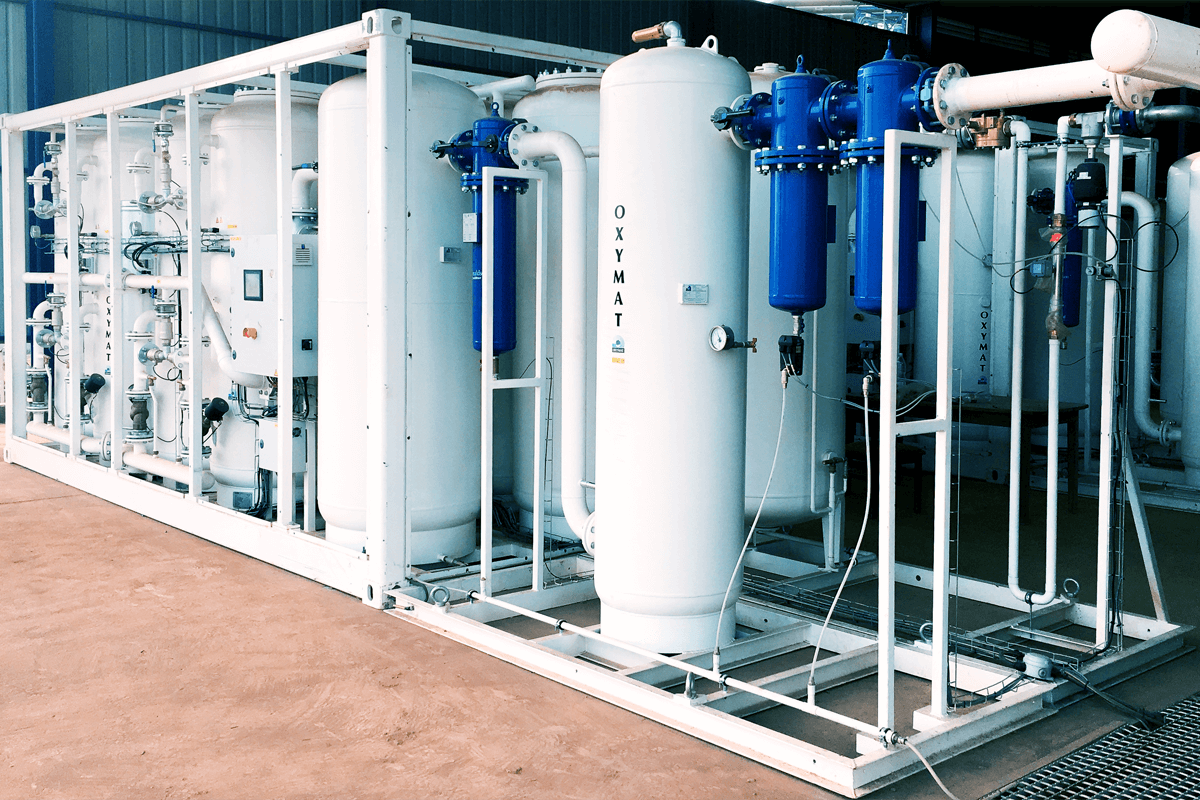
oxymat.com - mining
Post a Comment for "What Are The Considerations In Designing Electrical Systems For Mining And Mineral Processing?"